We are open to managing your modeling projects. Up to now we have completed a number of modeling commissions, the most important of which are presented in the summaries below.
Project 1
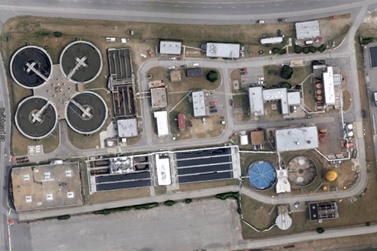
Background: The plant has primary treatment with occasional ferric addition, followed by a Five-Stage Bardenpho process configuration with carbon addition in the post anoxic tank. The plant also has a sidestream treatment for treating scrubber water generated from the incinerators.
Size: 34,000 m3/d, 74,000 PE
Modeling objectives and outcome:
- Perform solids mass balance around primary and secondary clarifiers
A significant mass balance error was identified in the primary clarifier solids data and corrected in the model. For secondary clarifiers, the coefficient of hindered settling was drastically reduced to 0.05 L/g to reproduce the solids in the underflow and coefficient of flocculant settling was increased to 20 L/g. This was to simulate effluent TSS which suggested fast settling solids.
- Model the aeration capacity of the plant
The specific standard oxygen transfer efficiency of about 39% was identified from the model which was comparable to the design.
- Confirm plant’s current carbon dosing strategy and impact of dissolved oxygen bleeding
An important lesson learned was the amount of methanol oxidized due to oxygen bleeding through the weir and surface intrusion was predicted by the model to be about 21%. This is significant amount of carbon required towards driving the oxygen concentrations down to achieve acceptable denitrification conditions. A proposal was set to identify appropriate strategy to reduce oxidation of methanol. This could be a potential for cost saving for the plant.
- Determine impact of tanks out of services on the plant’s bio-P performance
Multiple scenario analysis was performed to simulate the impact on bio-P performance. The high nitrate concentration of 1.5 to 3 mgN/L in the primary clarifier effluent due to high recycle from the sidestream treatment facility was identified to be the possible reason for reduction on bio-P performance.
Figure 1.1. WWTP model configuration.
Project 2
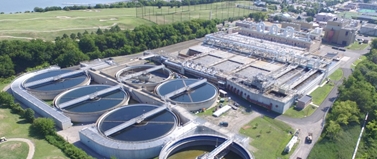
Background: The plant initially had a 3-stage biological treatment process, which provided bio-P and seasonal nitrification and denitrification. This was upgraded to a 5-stage process that provides year-round nite/denite, while maintaining bio-P performance as well.
Size: 92,000 m3/d, 300,000 PE
Modeling objectives and outcome:
- Reproduce current plant performance after the upgrade and investigate seasonal variation in bio-P performance
The modeled delivered successfully reproduced the solids and nutrient removal performance. The seasonal temperature changes from 13 °C to the 35 °C, which hampers Bio-P performance, especially during the summer season. The poor bio-P performance during the summer is attributed to shift in the biomass population. Using the advanced bio-P model in SUMO we can identify mitigation strategies to prevent poor bio-P performance.
- Optimizing air demand and carbon dose in post anoxic/aerobic zones while maintaining less than 5 mg N/L of effluent total nitrogen concentration
Two control logics were implemented and evaluated for operational optimization. Ammonia based aeration control and feed forward methanol addition control were implemented and multiple scenario analysis was performed with different ammonia and nitrate setpoints to identify minimum aeration demand and carbon requirements.
Figure 2.1. WWTP model configuration.
Figure 2.2. Predicted seasonal shift in PAO and GAO population.
Project 3
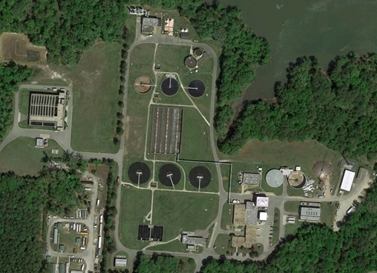
Background:The objective of this project was to build the full plant model of the WWTP and calibrate it to simulate summer and winter average conditions. The plant is operated as a plug flow reactor design, however prepared for step-feed operation. The main objective was to allow the model the evaluate the different operational strategies.
Size: 50,000 m3/d, 150,000 PE
Modeling objectives and outcome:
- Evaluate plug-flow and step-feed operational strategies
Simulate the impact on nitrification of the step-feed strategy into the last aerated tank. The model predicted lower MLSS in the reactor, thus it is highly likely that backmixing between the cells at the point of feeding distributes solids more evenly along the treatment train. This is more important when the plant operates in plug-flow configuration. The suggested operational transition between step-feed and plug flow can help the plant to optimize the disinfection in terms of efficiency and cost.
- Calibrate model parameters to meet predicted effluent ammonia
The calibrated model described the effluent ammonia concentrations during the switch between operational modes thus allowed the operators to fine tune the disinfection operational cost and properly predict the required dosage.
Figure 3.1. WWTP model configuration.
Figure 3.2. Predicted vs. measured effluent ammonia concentrations.
Project 4
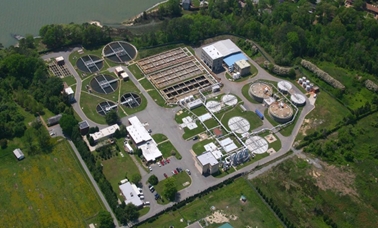
Background:The objective of this project was to build a full plant model and calibrate it to simulate one year of dynamic conditions.
Size: 47,000 m3/d, 200,000 PE
Modeling objectives and outcome:
- Impact of Sulphur
Based on the model results, the impact of considering sulphur species, especially on phosphorus removal and oxygen demand was evaluated.
- ABAC controller verification
The existing Ammonia Based Aeration Controller was verified to work similarly in the process model with or without the modelling of sulphur components thus allowing the investigation of various controller settings impact on the overall plant performance in terms of TN removal.
- IFAS unit performance overview to predict TN removal capacity
Verify and optimize mobile carrier model with addition of film and bulk SRT calculations, half saturations, and activity measurements compared to data to accurately investigate numerous aeration and recirculation strategies.
Figure 4.1. WWTP model configuration.
Figure 4.2. Predicted vs. measured effluent N concentrations.
Figure 4.3. Predicted vs. measured effluent P concentrations.
Project 5
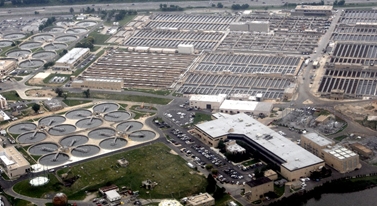
Background:The objective of this project was to build a full plant model and perform additional future model development to evaluate performance of new facilities and operational strategies.
Size: 1,400,000 m3/d, 3,125,000 PE
Modeling objectives and outcome:
- Describe the impact of technology upgrade
Thermal Hydrolysis Process model was used to evaluate digester startup and strategize future operation. The Filtrate Treatment Facility (FTF) commissioned in 2018. The model was calibrated on data from 2016 and FTF was added to the model as technology upgrade. The results were used to understand the impact of FTF on the whole plant operation.
- Oxygen transfer model verification
The aeration model was able to reproduce the average airflow rates in all the reactors, after minor adjustments were made to the alpha factors. The calibrated alpha factors are in the same range as measured experimentally.
- Iron dosage model verification
The iron model was verified by reproducing TP and OP in the primary, secondary, and final effluents. The model highlights the importance of mixing intensity at dosage points at the plant (currently low). The model also pointed towards the role of precipitate formation in the plant, especially in the digesters. Due to high iron dose, significant vivianite formation is predicted by the model.
- Investigate operational strategies
- High rate A-stage: A special model (SUMO 2C) has been developed that can predict primary, A-stage and final effluent colloids using an EPS based estimation.
- Partial Fe replacement by Alum: Omitting the iron dosing and replacing it with alum evidently stops vivianite and hydrous ferric oxide precipitation and instead Al(OH)3 and AlPO4 are formed.
Figure 5.1. WWTP model configuration.
Project 6
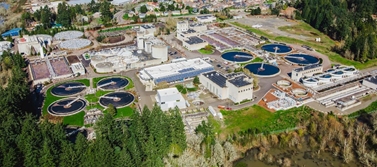
Background:The objective of this project was to build the model of two parallel treatment trains in a Water Resource Recovery Facility and optimize operational strategy for enhanced biological phosphorus removal (EBPR).
Size: 140,000 m3/d, 345,000 PE
Modeling objectives and outcome:
- Optimization of plant operation strategy
The configuration of the parallel aeration basins WRRF enables plant operation both in A2O and in Westbank side-stream EBPR modes. Modeling was used as a tool to select operational parameters, such as determining the optimal anaerobic detention time for RAS fermentation, in order to reach the best performance for the observed influent scenarios and operating conditions. The project shows a good example how utilities with flexible infrastructure can benefit from process model application.
Figure 6.1. WWTP model configuration.
Project 7
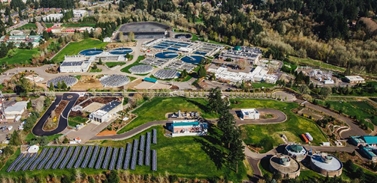
Background:The objective of this project was to build the full plant model of an advanced WWTP for operation optimization, with the goal of reducing chemical usage and enhancing phosphorus recovery.
Size: 98,000 m3/d, 375,000 PE
Modeling objectives and outcome:
- Optimization of plant operation strategy
This plant was among the first facilities in the United States to recover phosphorus using the Ostara struvite recovery system, whose product is an approved, marketable fertilizer. The purpose of modeling was to optimize plant operation in order to reduce alum usage and increase struvite production while maintaining good phosphorus removal rate in the liquid stream. The project is a good example of model application where process optimization helped to reduce operating costs and to raise revenue from product sales.
Figure 7.1. WWTP model configuration.
Project 8
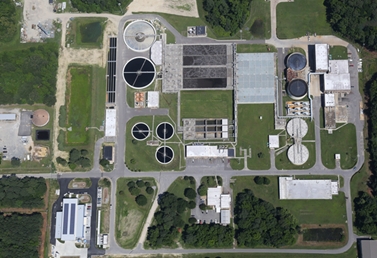
Background:The objective of the project was to develop a Digital Twin for real-time simulations and process control application of a 5-stage Bardenpho process configuration. The plant has Ammonia-Based Aeration Control (ABAC) implemented for achieving optimum aeration and nitrification performance.
Size: 60,000 m3/d, 250,000 PE
Modeling objectives and outcome:
- Identifying cost-effective aeration control strategies through real-time simulation
A fully calibrated full plant WWTP model is linked to the Emerson Ovation’s Open Platform Communication Unified Architecture (OPC-UA) through SUMO’s OPC-UA interface. The Digital Twin is setup to identify the dissolved oxygen setpoints to achieve ammonia setpoints based on a 24-hour average aerobic sludge retention time. The data communication, simulation and identification of setpoints are done in real-time, allowing the plant to achieve cost effective aeration control.
Figure 8.1. WWTP model configuration.
Project 9
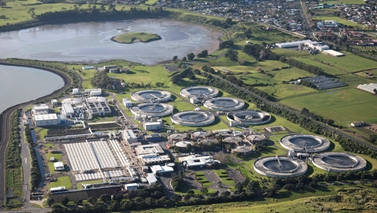
Background:The objective of this project was to build the full plant model of an existing WWTP and perform simulations of planned future developments in order to evaluate the performance of new facilities and operational strategies.
Size: 350,000 m3/d, 1,950,000 PE
Modeling objectives and outcome:
- AAA: Alternating Activated Adsorption implementation
The model version accurately represents the compact pre-treatment unit. It integrates all features of an A-stage in a dual-tank-configuration – biomass activation, biomass recycling, sludge wasting and waste sludge thickening, well suited to retrofit existing primaries at a hydraulic retention time of ca. 2 hours.
- AvN: Optimal N removal
The AvN model accurately describes the addition of ammonia versus nitrate control logic implementation to optimize aeration and carbon dosage.
- Implement inDENSE technology
The technology increases process throughput and performance through the selection of dense sludge aggregates. The model results reflect the improved settling rates and the promotion of enhanced biological phosphorus removal (EBPR).
- CAMBI technology for the solids treatment line
The developed thermal hydrolysis model accurately predicts the change in the solids treatment line.
- P recovery
CalPrex and AirPrex technology was evaluated and compared to provide information for the technology selection.
- Implement DEMON technology for sidestream treatment
The key is the proper mathematical representation of the sequenced process to achieve the accurate prediction of the N removal through the anammox shortcut processes.
With these technology upgrades a modern, energy neutral resource recovery facility can be built for the coming decades. The model provides whole plant mass balances and enables plant-wide performance assessment, impacts of each process addition on the whole plant and each other.
Figure 9.1. WWTP model configuration.